Yaskawa YRC1000
Yaskawa YRC1000
Home > Yaskawa > Controllers > YRC1000
Overview
The MOTOMAN YRC1000 stands out as a compact yet robust controller platform, designed to handle complex multi-axis and multi-tasking operations for both robots and associated peripheral equipment. With the capability to coordinate the movements of up to 8 robots (Master/Slave setup) and additional external axes, totaling up to 72 motion axes, the YRC1000 proves itself indispensable in various industrial applications. It finds compatibility with a wide range of MOTOMAN robots, including the GP-Series handling and spot welding robots, AR-Series arc welding robots, HC-Series cobots, and PL-Series Palletizers.
Operation
The YRC1000 offers a user-friendly interface, catering to both seasoned professionals and newcomers to robotics. Equipped with either a standard Teach Pendant featuring a touchscreen for advanced users or the intuitive Smart Pendant tailored for beginners, the controller streamlines operation and programming. Drawing from extensive field experience and feedback from over 500,000 deployed robots, MOTOMAN has refined the operational concept, resulting in a highly efficient environment characterized by simple menu structures, quick access to teach positions, and easy-to-understand program structures. Advanced users can leverage the power of the Inform III language to craft intricate commands or develop custom motion and communication functions. User rights management is simplified through a modern USB Stick system.
Motion Control Technology
Powered by a high-speed multitasking CPU, an advanced operating system, and Yaskawa Sigma7 servo technology, the YRC1000 ensures swift accelerations, fast axis speeds, and precise path performance. Its multitasking, non-Windows-based operating system operates with rapid interpolation cycles, eliminating the need for extensive virus protection measures. This results in a boot time of under 40 seconds. The Advanced Robot Motion (ARM) function dynamically manages torque and load, optimizes acceleration and speed, suppresses vibrations, and enables precise collision detection. Various interpolation methods and path switching functions allow for precise definition and execution of robot paths. An integrated soft PLC facilitates control of peripherals or smaller production cells, potentially obviating the need for a separate PLC cell controller.
Controller Hardware
Featuring a modular design, the YRC1000 ensures easy component replacement, minimizing downtime. Its compact, industry-proof cabinet boasts an IP54 rating and an indirect cooling system, making it suitable for demanding industrial environments. Each robot cabinet provides space for up to 3 external axis controllers. A range of cabinet sizes accommodates additional external axes, interfaces, fieldbus systems, safety systems, and third-party application controllers.
Functions and Function Packages
The YRC1000 offers a plethora of function packages catering to various applications, including handling, arc welding, spot welding, and painting. Additionally, it provides single functions such as Servofloat, Machine Vision, and Analog Control, enhancing programming and commissioning convenience.
Machine Safety
With a two-channel safety system architecture and onboard Functional Safety Board, the YRC1000 ensures safe I/O communication. Safety devices like scanners or light barriers can be directly wired to the controller, while all Teach Pendants feature obligatory 3-position enabling switches. Robot servo motors employ high-precision absolute encoders and spring-operated brakes for enhanced safety.
Functional Safety Software Options
The Functional Safety Software enables precise monitoring of position and speed within defined workspace zones, allowing for the modeling of complex cell layouts and interactions. It considers the complete mechanical structure of the robot, enhancing safety and efficiency.
Energy Efficiency
Utilizing the latest YASKAWA Sigma7 servo drive technology, the YRC1000 enhances the energy efficiency of MOTOMAN robots. Energy-saving options such as Individual Servo-Off and condenser-based recuperation units further contribute to energy savings, particularly in applications involving short motion sequences and frequent decelerations like spot welding.
Open Communication
The YRC1000 supports seamless integration into existing networks, boasting standard communication interfaces like Ethernet ports and digital inputs/outputs. It also supports protocols for Industry 4.0, facilitating connectivity and interoperability.
Open Programming
MOTOMAN Robots with YRC1000 controllers support various programming methods, catering to diverse applications and environments. From standard Teach Pendants to offline simulation tools and third-party CAD/CAM software, users have the flexibility to choose the programming approach that best suits their needs. Additionally, the controller supports hardware programming devices and interfaces with scientific PC programming environments, enabling advanced customization and integration.
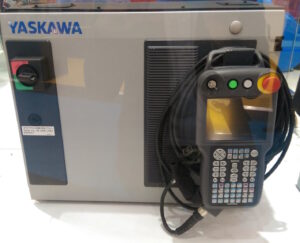