Yaskawa FS100
Home > Yaskawa > Controllers > FS100
Yaskawa FS100
Introduction The FS100
The FS100 stands out as a robust and precise open robot controller, meticulously crafted for High-Speed Pick & Place tasks and seamless integration into packaging lines. Its compact footprint and lightweight construction make it a perfect fit for space-saving standalone setups or versatile installation within machine control cabinets, whether horizontally or vertically.
Performance
This controller embodies a blend of compactness, power, and openness, tailored specifically for packaging, small parts handling, and assembly applications. With its exceptional performance tailored for high-speed, discrete operations, coupled with an open software architecture, it empowers OEMs, machine builders, and system integrators to fashion bespoke software solutions to suit their needs.
Design
Crafted with precision for Motoman® robots with payloads up to 20 kg, the FS100 prioritizes space efficiency without compromising performance. Its small, compact design measuring 470 mm wide, 200 mm high, and 420 mm deep, alongside a standard IP20 cabinet (with an optional IP54 enclosure), ensures durability and adaptability across various environments, all while weighing approximately 20 kg.
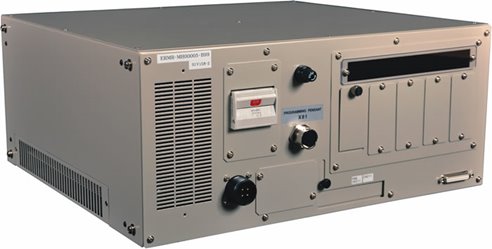
System
Equipped with a Touch Screen Teach Pendant, the FS100 controller embodies the culmination of years of refinement and optimization in MOTOMAN robot operation. Drawing from the invaluable experience and feedback garnered from over 500,000 robots deployed in various fields, it delivers a remarkably efficient operational and programming environment. Powered by a multitasking, non-Windows-based operating system, the FS100 operates with a rapid interpolation cycle, obviating the need for virus protection and alleviating the burdensome efforts associated with frequent updates and maintenance. Boasting a boot time of under 40 seconds, it ensures swift deployment and operational readiness. The FS100 presents a diverse array of functions, including Servofloat and Machine Vision, simplifying the programming and commissioning endeavors of MOTOMAN robots and their peripherals. Each function contributes to a comfortable and straightforward user experience, enhancing overall operational efficiency.
Safety
Prioritizing safety, the FS100 adopts an MSU safety system architecture, incorporating Emergency Stop and Safety Signals to facilitate secure I/O communication. Featuring obligatory 3 position enabling switches on the Teach Pendant, it ensures adherence to safety protocols. Furthermore, equipped with high-precision absolute encoders and spring-operated brakes, all robot servo motors seamlessly engage in the event of an emergency stop, obviating the need for cyclical brake tests and enhancing overall safety standards.
Connectivity and Integration
With enhanced communication speeds and functionality, the FS100 outpaces the DX100 controller by 2-4 times. It seamlessly integrates with optional MotoSight™ 2D vision for added versatility and supports rapid I/O response, precise high-resolution timers, and an extensive array of communication networks. Versatility is further highlighted as a single FS100 controller can manage up to eight axes, accommodating diverse configurations such as 4-axis robot + 2 external axes, 6-axis robot + 2 external axes, and 7-axis robot + 1 external axis. For systems requiring 15 axes, two FS100 controllers are necessary.
Software Customization
In the realm of software, the FS100 shines with its open architecture, facilitating seamless customization in widely accepted environments like C, C++, C#, and .NET. It seamlessly integrates optional MotoPlus™ and MotomanSync™ software, utilizing the same programming pendant hardware as the DX100 controller for a consistent interface with existing products. Moreover, customization of programming pendant screens using C++ and C# is fully supported.
Networking Capabilities
Integration into existing networks is effortless with the FS100. Equipped with standard communication interfaces including Ethernet and USB ports, digital inputs/outputs, and an FTP-capable TCP/IP web server function, it enables remote monitoring and maintenance over the Web, ensuring seamless connectivity. Supporting an extensive range of fieldbus systems such as Ethernet-IP, Ethercat, Profinet, Profibus, and CCLink, the FS100 enhances flexibility with direct or fieldbus-based communication interfaces for a myriad of peripheral devices and equipment. This integration is often complemented by HMI integration on the teach pendant, facilitating seamless operation with various grippers, 2D/3D Vision Systems, or Force/Torque Sensors.
Soures: Yaskawa.com Motoman.com